Plastic extrusion for complex profiles and custom designs
Plastic extrusion for complex profiles and custom designs
Blog Article
A Comprehensive Overview to the Refine and Advantages of Plastic Extrusion
In the substantial realm of manufacturing, plastic extrusion arises as a extremely reliable and necessary process. Transmuting raw plastic right into continuous profiles, it satisfies a wide variety of industries with its impressive adaptability. This guide intends to clarify the complex actions associated with this approach, the types of plastic suitable for extrusion, and the game-changing benefits it offers the industry. The taking place discussion guarantees to unravel the real-world impacts of this transformative process.
Recognizing the Essentials of Plastic Extrusion
While it may appear facility at very first glimpse, the process of plastic extrusion is essentially basic. The procedure begins with the feeding of plastic product, in the kind of powders, granules, or pellets, right into a heated barrel. The designed plastic is then cooled, solidified, and reduced right into desired sizes, finishing the procedure.
The Technical Process of Plastic Extrusion Explained
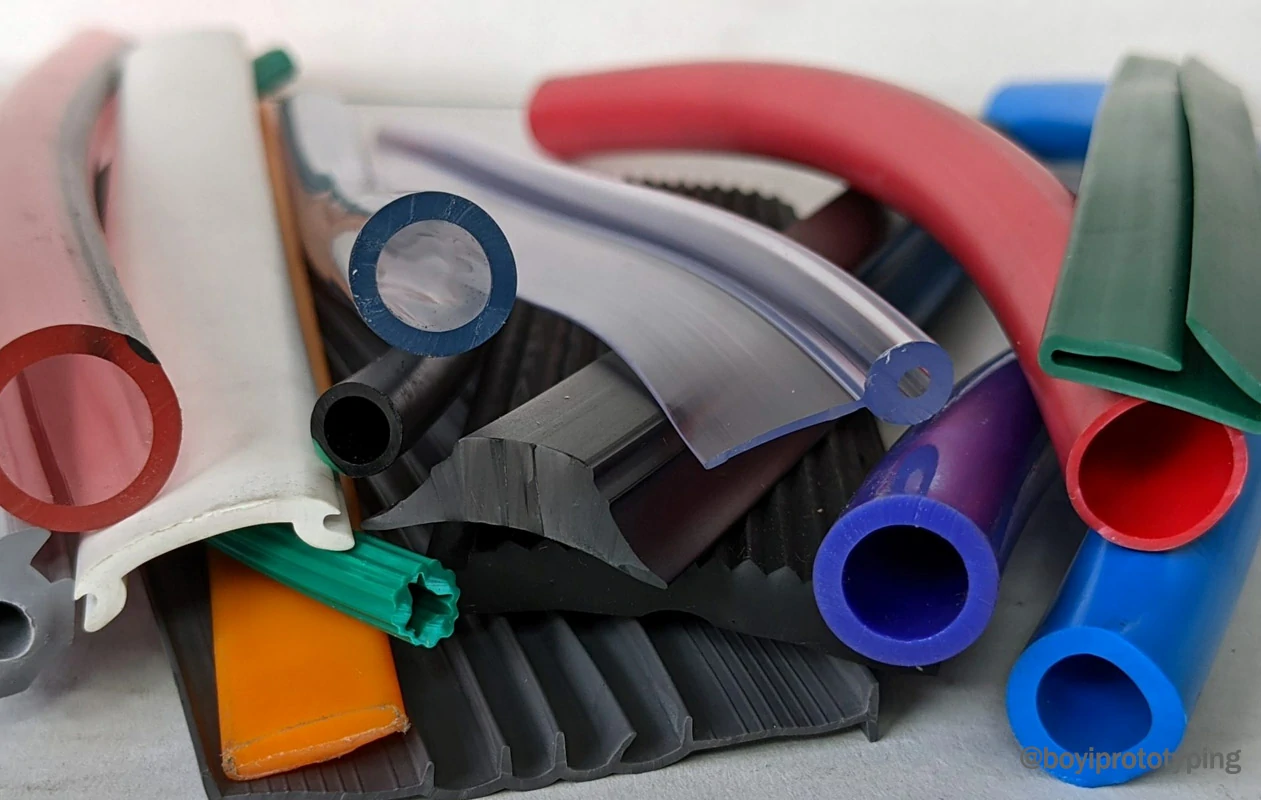
Sorts Of Plastic Suitable for Extrusion
The selection of the best kind of plastic is a critical facet of the extrusion procedure. Different plastics offer unique buildings, making them a lot more matched to certain applications. Understanding these plastic kinds can considerably enhance the extrusion procedure.
Comparing Plastic Extrusion to Various Other Plastic Forming Methods
Recognizing the sorts of plastic suitable for extrusion paves the way for a more comprehensive discussion on just how plastic extrusion stacks up versus other plastic creating methods. These consist of injection molding, blow molding, and thermoforming. Each method has its distinct uses and benefits. Injection molding, for example, is excellent for producing intricate parts, while impact molding is perfect for hollow items like containers. Thermoforming excels at forming big or superficial components. However, plastic extrusion is unrivaled when it involves creating constant profiles, such as gaskets, seals, and pipes. It also enables a regular cross-section along the size of the product. Therefore, the choice of technique mainly relies on the end-product requirements and specifications.
Secret Benefits of Plastic Extrusion in Manufacturing
In the realm of manufacturing, plastic extrusion provides numerous considerable advantages. One notable advantage is the cost-effectiveness of the process, that makes it a financially enticing manufacturing technique. Furthermore, this method gives premium item adaptability and boosted production rate, consequently boosting total manufacturing effectiveness.
Economical Manufacturing Approach
Plastic extrusion leaps to the leading edge as a cost-efficient manufacturing method in production. This process attracts attention for its capability to generate high volumes of product rapidly and successfully, supplying manufacturers with considerable savings. The main expense benefit is the capacity to use more economical raw materials. Extrusion makes use redirected here of polycarbonate products, which are much less expensive compared to metals or porcelains. Further, the extrusion procedure itself is relatively straightforward, minimizing labor prices. Additionally, plastic extrusion needs much less power than conventional production approaches, adding to lower functional costs. The procedure also minimizes waste, as any kind of malfunctioning or see it here excess materials can be reused and recycled, supplying another layer of cost-effectiveness. Generally, the financial benefits make plastic extrusion an extremely eye-catching option in the manufacturing industry.
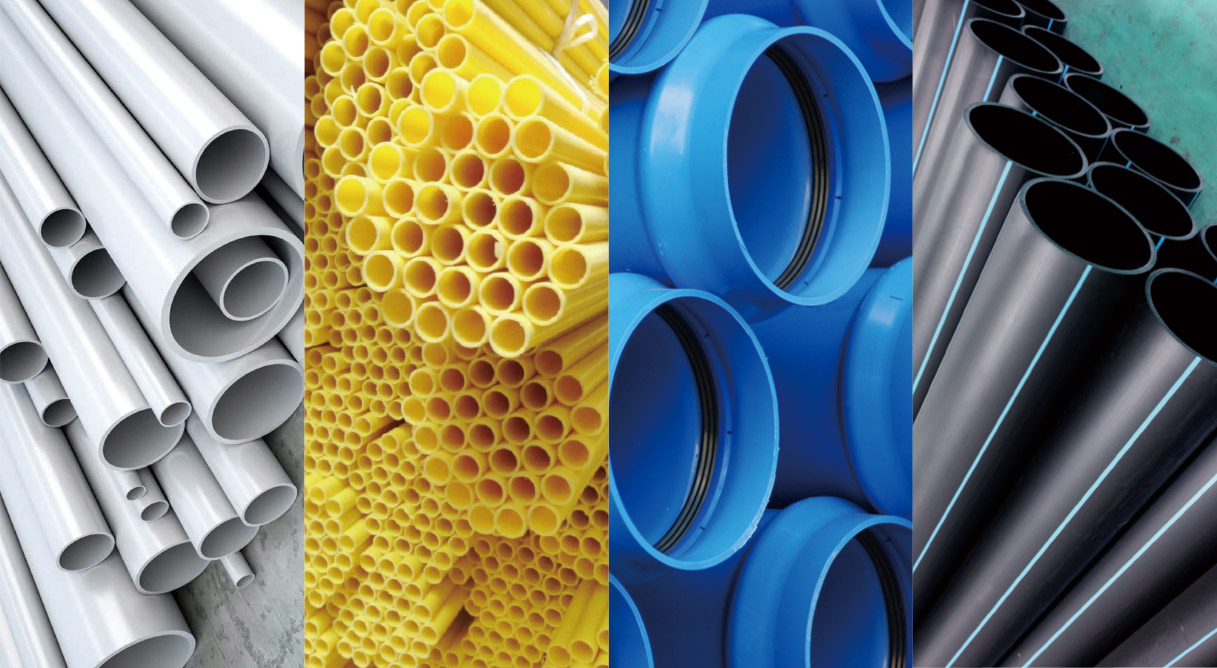
Superior Product Flexibility
Beyond the cost-effectiveness of plastic extrusion, an additional significant benefit in making lies in its remarkable item flexibility. This makes plastic extrusion a perfect remedy for markets that require personalized plastic components, such as vehicle, construction, and product packaging. In essence, plastic extrusion's item versatility cultivates development while boosting operational performance.
Boosted Manufacturing Speed
A considerable benefit of plastic extrusion exists in its boosted manufacturing speed. Couple of various other manufacturing processes can match the rate of plastic extrusion. Furthermore, the capability to maintain regular high-speed manufacturing without compromising product quality sets plastic extrusion apart from other methods.
Real-world Applications and Effects of Plastic Extrusion
In the realm of production, the strategy of plastic extrusion holds extensive relevance. The financial benefit of plastic extrusion, largely its cost-effective and high-volume outcome, has changed production. The industry is persistently striving for developments in recyclable and naturally degradable materials, suggesting a future where the benefits of plastic extrusion can be maintained without jeopardizing ecological sustainability.
Final thought
In conclusion, plastic extrusion is a effective and very effective approach of transforming resources right into diverse products. It offers countless benefits over other plastic creating techniques, including cost-effectiveness, high result, very little waste, and layout flexibility. Its impact is greatly really felt in numerous sectors such as building, automobile, and customer products, making it a view publisher site pivotal process in today's production landscape.
Digging deeper right into the technical process of plastic extrusion, it begins with the choice of the proper plastic material. When cooled down, the plastic is reduced into the called for sizes or wound onto reels if the product is a plastic movie or sheet - plastic extrusion. Contrasting Plastic Extrusion to Other Plastic Forming Methods
Recognizing the types of plastic suitable for extrusion paves the way for a broader conversation on just how plastic extrusion stacks up versus other plastic developing techniques. Few various other manufacturing procedures can match the rate of plastic extrusion.
Report this page