Plastic extrusion for thermoplastics, PVC, and engineering plastics
Plastic extrusion for thermoplastics, PVC, and engineering plastics
Blog Article
Recognizing the Essentials and Applications of Plastic Extrusion in Modern Production
In the world of modern production, the strategy of plastic extrusion plays an important role. Unraveling the basics of this process exposes the true flexibility and possibility of plastic extrusion.
The Basics of Plastic Extrusion Refine
While it might appear complex, the principles of the plastic extrusion procedure are based upon relatively simple concepts. It is a manufacturing process where plastic is thawed and after that shaped right into a constant account via a die. The raw plastic material, typically in the type of pellets, is fed right into an extruder. Inside the extruder, the plastic undergoes warmth and pressure, creating it to thaw. The liquified plastic is after that compelled via a designed opening, understood as a die, to form a long, continuous product. The extruded product is cooled and after that reduced to the wanted size. The plastic extrusion process is thoroughly used in numerous industries because of its cost-effectiveness, effectiveness, and versatility.
Different Types of Plastic Extrusion Strategies
Building upon the fundamental understanding of the plastic extrusion process, it is needed to check out the various techniques entailed in this production approach. The two key methods are profile extrusion and sheet extrusion. In profile extrusion, plastic is thawed and formed into a continuous account, commonly used to create pipes, rods, rails, and home window frames. In contrast, sheet extrusion creates big, level sheets of plastic, which are generally more processed into products such as food packaging, shower curtains, and automobile components. Each method calls for specialized equipment and precise control over temperature level and pressure to guarantee the plastic preserves its shape throughout air conditioning. Understanding these strategies is key to utilizing plastic extrusion properly in modern manufacturing.

The Function of Plastic Extrusion in the Automotive Market
An overwhelming bulk of parts in modern-day lorries are products of the plastic extrusion process. This process has reinvented the vehicle market, changing it into a more efficient, cost-efficient, and adaptable manufacturing sector. Plastic click reference extrusion is mainly used in the production of various auto components such as bumpers, grills, door panels, and dashboard trim. The process offers an attire, constant outcome, enabling makers to generate high-volume get rid of terrific precision and marginal waste. The lightness of the extruded plastic parts adds to the total decrease in automobile weight, improving gas performance. The sturdiness and resistance of these parts to heat, chilly, and impact improve the longevity of cars. Therefore, plastic extrusion plays view website a crucial function in automotive manufacturing.
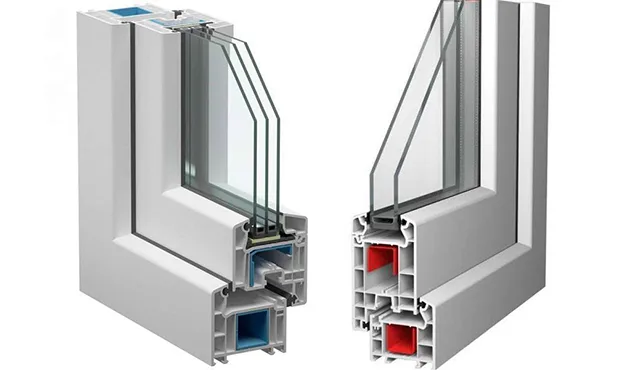
Applications of Plastic Extrusion in Durable Goods Manufacturing
Past its substantial impact on the auto market, plastic extrusion shows similarly effective in the world of durable goods manufacturing. This procedure is essential in producing a vast range of products, from food product packaging to family home appliances, playthings, and even clinical gadgets. The versatility of plastic extrusion allows makers to create and generate intricate sizes and shapes with high precision and efficiency. Furthermore, because of the recyclability of numerous plastics, squeezed out components can be recycled, lowering waste and cost. The adaptability, adaptability, and cost-effectiveness of plastic extrusion make it a favored selection for several consumer products suppliers, contributing dramatically to the sector's development and innovation. However, the environmental useful link effects of this widespread use need mindful consideration, a topic to be discussed better in the subsequent area.
Environmental Influence and Sustainability in Plastic Extrusion
The prevalent use of plastic extrusion in manufacturing invites examination of its ecological ramifications. Reliable machinery reduces power usage, while waste administration systems recycle scrap plastic, lowering raw product demands. Regardless of these improvements, better technology is needed to minimize the ecological footprint of plastic extrusion.
Verdict
In verdict, plastic extrusion plays an essential function in modern-day manufacturing, particularly in the auto and consumer products fields. Recognizing the basics of this process is essential to maximizing its applications and benefits.
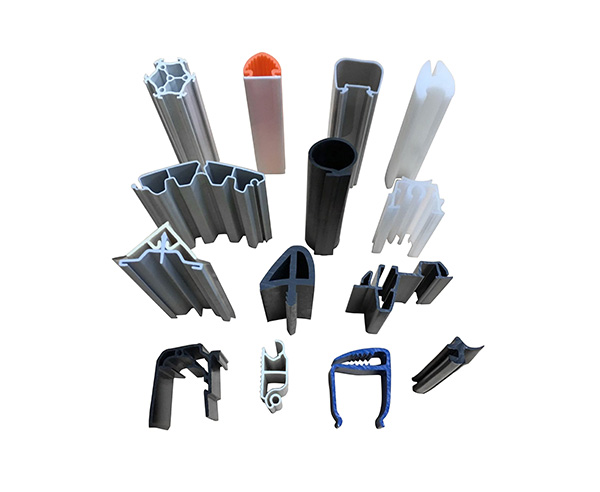
The plastic extrusion procedure is thoroughly utilized in various industries due to its cost-effectiveness, convenience, and performance.
Structure upon the fundamental understanding of the plastic extrusion procedure, it is necessary to check out the various techniques entailed in this production technique. plastic extrusion. In contrast, sheet extrusion develops huge, flat sheets of plastic, which are normally more refined into items such as food product packaging, shower drapes, and vehicle components.An overwhelming majority of parts in modern-day automobiles are items of the plastic extrusion procedure
Report this page